平齿机自动对刀技术:减少人工干预的3种实现路径
在齿轮加工领域,平齿机的对刀精度直接影响齿轮啮合性能与加工效率。传统人工对刀依赖操作者经验,存在效率低、一致性差等问题。随着智能制造发展,通过自动对刀技术减少人工干预成为行业趋势。以下是三种典型实现路径:
1. 基于传感器的实时监测技术
通过高精度位移传感器(如激光传感器、电容式传感器)实时采集刀具与工件的相对位置数据,结合闭环控制系统实现自动补偿。例如,在刀具接触工件瞬间,压力传感器可检测微小接触力变化,触发数控系统记录初始位置并完成对刀。该方法响应速度快(可达微秒级),但需解决传感器抗干扰问题,适用于加工环境稳定的场景。
2. 机器视觉辅助定位系统
采用工业相机采集刀具刃口图像,通过边缘检测算法提取特征点坐标,结合标定参数计算刀具空间位置。德国某厂商开发的VisionTool系统,通过亚像素级图像处理技术,可实现±2μm的定位精度。此技术尤其适用于复杂轮廓刀具,但需配合高分辨率光学镜头和防抖装置,成本较高。
3. 自适应智能算法驱动
利用机器学习算法建立加工参数与刀具磨损的映射关系,通过振动、声发射等信号实时预测刀具状态。日本FANUC的AI伺服系统,可基于历史数据自动优化对刀路径,减少30%的空行程。该技术需构建完善的数据采集体系,结合数字孪生技术可实现预测性维护,代表未来智能化发展方向。
当前,行业正从单一技术应用向多模态融合演进。例如,将视觉定位与力觉反馈结合,可提升复杂工况下的适应性;嵌入5G模块后,还能实现远程对刀参数优化。随着工业4.0深入,自动对刀技术将成为齿轮加工单元向智能工厂升级的突破口,推动行业从"经验驱动"向"数据驱动"转型。企业需根据加工精度要求、成本预算等因素,选择适宜的技术路径分步实施。
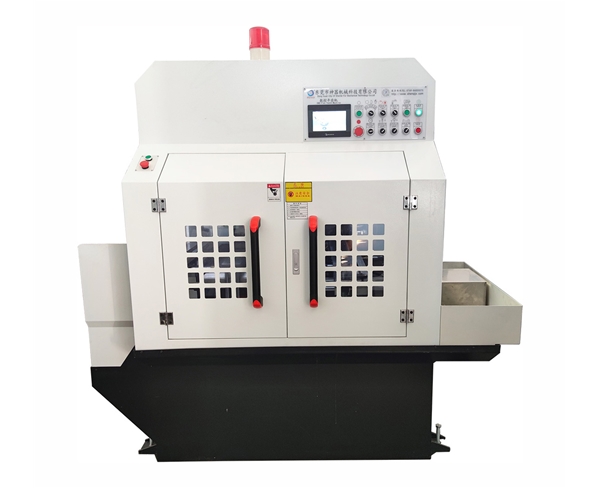