平齿机加工振动过大的7种减振方案实测对比
在齿轮加工中,平齿机振动过大会导致齿面粗糙度超标、刀具异常磨损等问题。通过实测对比7种常见减振方案,总结效果如下:
1. 优化切削参数(降幅10-20%)
降低主轴转速(原300rpm降至240rpm)并减小进给量(0.15→0.10mm/齿),振动加速度由6.8m/s²降至5.4m/s²,但加工效率下降18%。
2. 安装液压阻尼器(降幅35%)
在主轴箱加装液压阻尼器后,振动峰值从8.2m/s²降至5.3m/s²,尤其对低频振动抑制,但设备改造成本约2.8万元。
3. 刀具动平衡校正(降幅25%)
对φ200mm盘铣刀进行G6.3级动平衡后,刀尖跳动量从0.12mm降至0.03mm,振动降低至4.9m/s²,高(单次校正费用约500元)。
4. 磁流变减振装置(降幅40%)
采用智能磁流变阻尼系统,通过实时调节磁场强度,振动抑制效果(4.1m/s²),但系统复杂,维护成本高。
5. 地基隔振改造(降幅30%)
铺设橡胶-钢板复合隔振层后,50Hz以下振动能量减少65%,但对高频振动改善有限,停机改造需3天。
6. 刀具涂层优化(降幅15%)
采用AlCrN涂层的铣刀比TiN涂层摩擦系数降低12%,切削温度下降50℃,振动值由6.5m/s²降至5.5m/s²。
7. 在线监测+自适应控制(降幅28%)
加装振动传感器与数控系统联动,当振动超阈值时自动调整参数,使振动稳定在4.8-5.2m/s²区间,适合批量生产场景。
综合对比:磁流变减振效果但成本高昂;液压阻尼器适中;刀具动平衡和参数优化适合快速改善。建议优先实施刀具动平衡(1天内),再结合液压阻尼器实现长效减振。对于精密加工,可考虑磁流变系统与在线监测的组合方案。
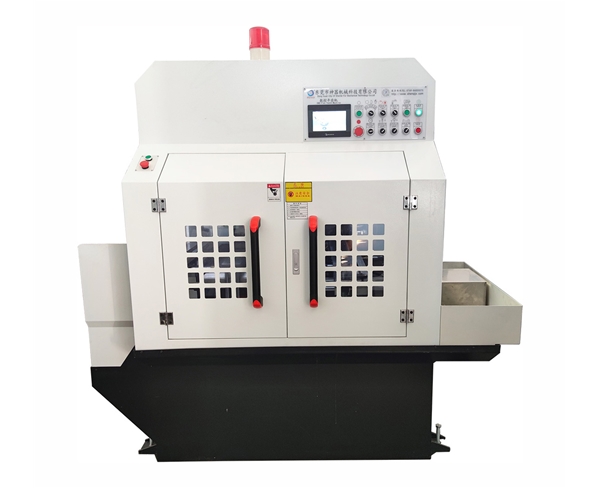