数控平齿机闭环控制系统解析:误差补偿技术详解
数控平齿机作为高精度齿轮加工设备,其闭环控制系统通过误差补偿技术实现对加工精度的动态优化。闭环系统由传感器、控制器和执行机构组成,通过实时监测加工误差并动态调整参数,形成“检测-反馈-修正”的闭环控制逻辑,有效突破传统开环系统的精度瓶颈。
误差补偿技术主要分为两类:
1. 静态误差补偿:针对机床几何误差(如导轨直线度、丝杠螺距误差)、热变形误差及刀具磨损误差,通过离线标定建立误差映射模型,利用数控系统预设补偿值。例如,激光干涉仪标定丝杠误差后生成补偿曲线,通过反向插补修正轨迹。
2. 动态实时补偿:基于在线监测系统(如光栅尺、编码器)实时采集位置/振动信号,结合加速度传感器监测切削力扰动。采用PID控制算法或模糊神经网络算法,对伺服电机扭矩、进给速度进行即时调整。特别在高速加工时,可同步补偿热误差和切削变形误差。
系统采用多源误差融合补偿策略:通过温度传感器网络构建机床热场模型,结合振动频谱分析优化切削参数,实现误差补偿量动态修正。某实验数据显示,采用复合误差补偿技术后,齿形误差可降低50%-70%,齿向误差控制在3μm以内。
未来发展趋势将结合数字孪生技术,构建虚实联动的预测性补偿系统,进一步提升平齿机在智能制造场景下的加工精度与稳定性。
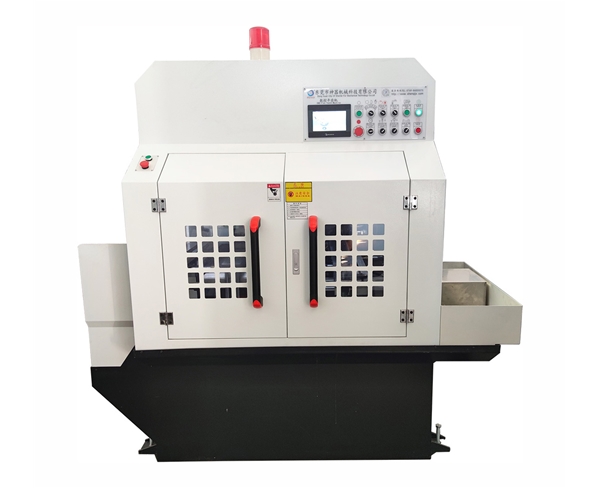